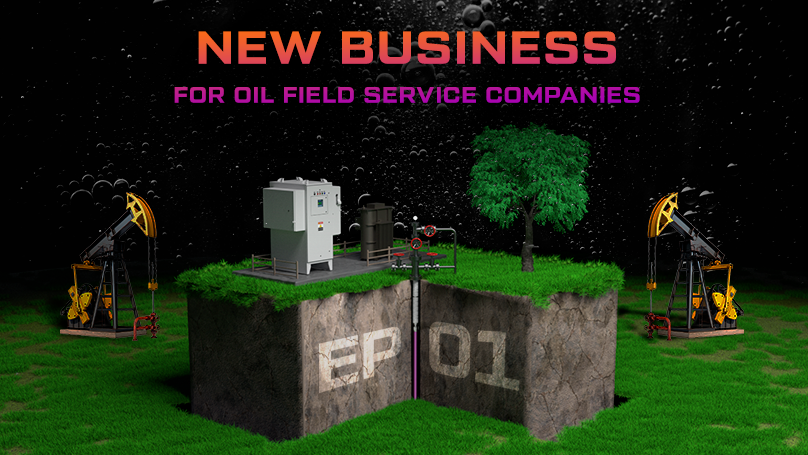
As we wrote earlier, the life cycle of a well is divided into two stages:
Stage I - operation at a flow rate of more than 300 bpd; and
Stage II - operation at flow rates less than 300 bpd.
According to the U. S. Energy Information Administration (EIA), at the end of 2020 the number of wells with flow rates of less than 15 barrels of oil equivalent per day (BOE/d) was 80% of the US well stock.
According to EIA data, the percentage has not changed from 2000 to 2020. Still, given the increase in the total number of wells, we can say that the number of low-rate wells will increase, which in turn requires oil field service companies and oil companies to review the costs of operating low-rate well stock, as the share of revenues from these wells will increase. For oil field service companies, which produce only from high-rate wells, it is necessary to pay attention to the growth of production volumes from wells with productivity below 300 bpd, in order to increase the company's profits.
Triol offers a complete solution that not only increases production efficiency when operating low-rate wells, but also reduces costs when switching from ESP production technology, which serves as the main technology for high-rate wells.
Table 1 shows a comparison in equipment and associated losses for different technologies for stages I and II of the life cycle of wells:
Table 1 - Comparative characteristics of technologies
Based on Table 1, we can conclude that the technology of sucker-rod pumping, which is most widespread now in the operation of low-rate wells, requires significant investments associated with it:
- increase in the number of nomenclatures and their uniqueness, not being able to use the nomenclatures that were used for ESP, while EP01 allows the use of similar auxiliary equipment;
- the need for additional personnel and more frequent inspections; and
- expansion of storage facilities.
Let's take a closer look at these differences compared to ESP and EP01.
Increasing the number of nomenclatures
Figure 1 shows the schematic layout of the SRP, ESP and EP01, where you can visually assess the differences in technology and compare the number of unique and unified elements.
Figure 1 - System layout:
a) SRP; b) ESP; c) EP01.
Personnel and Service
When using the SRP for oilfield service companies and oil companies, it is necessary to have an additional group of mechanics servicing the ground equipment mechanisms, whose tasks include inspection of:
- the condition of the belts;
- augers;
- cables;
- gland seals;
- the condition of the braking system; and
- the condition of the gearbox.
The time of these works can range from 30 minutes to several hours, if necessary, to perform a replacement or repair of the equipment.
Figure 2 - Consumables:
- Strap
- Brake pads
- Suspension cable
- Gland seal
If you look at EP01, you can highlight advantages such as:
- there is no need for additional training of personnel in the installation of surface and submerged equipment, since the process is similar to ESP;
- the software has algorithms for the automated extraction process, which reduces training to a few days;
- the lack of monthly well maintenance due to the lack of mechanical parts and remote control over the parameters of equipment operation; and
- no mechanical ground equipment, thus reducing the mechanical maintenance team.
Warehouse space
A separate cost item is the additional storage space for the equipment. Table 2 shows the space required to store 10 sets of ESP (pumps, motors, VSD), ЕР01 (pumps, motors, VSD), given the stacking of pumps and motors in 5 tiers, and SRP (rocking machines). Figure 3 illustrates the storage of pumps and motors for ESP, ЕР01, and the rocking machine for SRP.
Table 2 - Comparison of storage areas of ESP, ЕР01, SRP
a)
b)
Figure 3 - Storage: a) ESP, EP01; b) SRP (rocking machine).
To summarize, let's highlight the main advantages of Triol's offerings:
-
Reducing costs when switching from ESP to oil production technology from wells with flow rates up to 300 bpd for oil and oilfield service producers operating a full cycle well with ESP and SRP;
-
Increase of profit due to additional operation of 80% of the well stock for oil companies and oilfield service companies operating wells only at the ESP stage;
-
The technology is based on familiar elements for the operating personnel. EP01 is similar to ESP for onshore equipment, which has only the control unit and transformer, and as a submerged part - only the motor and the pump;
-
No consumables during operation;
-
Interchangeability of transformers and equipment for installation and operation;
-
There is no need for additional personnel training on the installation of the surface and submersible equipment because the process is similar to ESP, and the software has algorithms for automated production process, i.e., switching to EP01 equipment allows one to avoid monthly maintenance of wells;
-
No mechanical ground equipment, thus reducing the mechanical maintenance team;
-
Reduced storage space compared to SRP. For example, only 18.4 sq. m are needed to store 10 sets of EP01.
Product development to reduce costs Triol continues to develop the product and is currently working on theoretical studies for the use of the VSD for ESP and EP01. Thus, to switch to production with EP01, you will only need to change the control software, which will halve the cost of buying frequency converters.
Triol - Opening new horizons for your business.
subscribe.el.title
- Product news
- Events
- Discounts